26. September 2024 By Daniel Spieker
Data as the key to effective quality management
Experience shows that quality management systems (QM systems) lead a shadowy existence in many companies. Instead of actively contributing to the improvement of processes and products, their purpose is often merely to fulfil standards and maintain certifications. In this blog post, I will show how the effective use of data can increase the effectiveness of QM systems and what possibilities modern digital tools offer in this regard.
Although many quality managers want the QM system to be alive and effective, in practice it often looks quite different. Although specifications such as process descriptions, checklists or work instructions and verification documents such as test logs are available, they play a subordinate role in the company's day-to-day business. Their primary purpose is to document the company's processes so that it can present something during the regular audits and maintain existing certifications.
Let's look at two typical statements from QM audits:
‘We have documented our processes in detail!’
Standard compliance: Given.
Benefit for the company: Low to manageable.
The documentation of processes helps to create and maintain standards in procedures. However, the mere documentation of processes does not guarantee that they are up-to-date and that the desired standards are consistently maintained.
‘Tests that have been carried out are consistently recorded and the results are documented!’
Fulfilment of standards: Given.
Benefit for the company: Low to manageable.
The random execution and documentation of tests reduces the risk of non-conformities and complaints. However, a more in-depth analysis of the recorded data is required to identify patterns and weak points and to continuously improve products and processes on this basis.
These examples show that QM activities and documentation are often less aimed at improving operational processes and more at providing evidence of compliance with standard requirements. The QM system does not achieve the desired effectiveness in this way.
Quality management and data – an effective combination
‘Fact-based decision-making’ has been a central principle of relevant standards such as DIN EN ISO 9001 for years. This means that decisions should be based on figures, data and facts. It therefore requires the collection and analysis of data. The more data is available and the better its quality, the greater its benefit in decision-making.
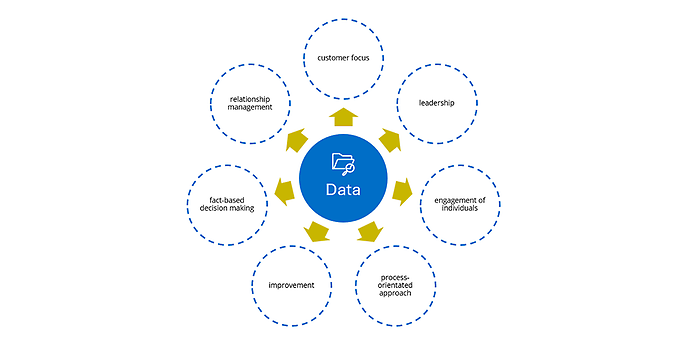
In addition to fact-based decision-making, there are other key principles in quality management. Let us also consider their connection to the collection, analysis and use of data:
- The requirements and expectations of external stakeholders can be evaluated on the basis of data and active relationship management can be implemented.
- Data enables the quantification and monitoring of customer expectations in order to ensure customer orientation and sustainable success.
- Management and leadership of employees is facilitated by deriving measurable goals from the strategy, defining measures and evaluating goal achievement based on data.
- Data empowers employees to make the right decisions and to objectively evaluate goal achievement. This enables measurable success and increases the motivation (engagement) of the workforce.
The process-oriented approach requires systematic monitoring and control of processes – data provides insights into process performance and helps to make fact-based adjustments.
Well-founded analyses of collected data show potential for improvement and are the basis for continuous improvement.
The more data-driven the quality management, the higher the efficiency.
There is a positive correlation between the effective use of data and all quality management principles. In terms of the overall quality management system, this means nothing other than that the more data-driven a company is, the greater its efficiency.
Data plays a central role in measuring, monitoring and continuously improving the quality of products, processes and services. They are enablers for effective quality management that not only exists on paper but also sustainably improves corporate performance.
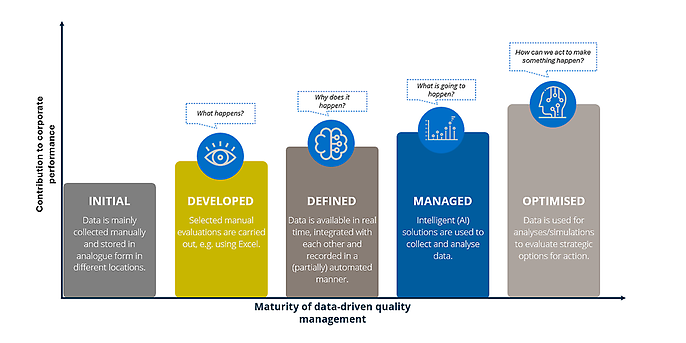
We distinguish between different levels of maturity. At an initial level, data is largely collected manually and processed in analogue form. Data is not linked, isolated data silos are available to limited user groups. Accordingly, options for evaluation are severely limited.
At the ‘developed’ level of maturity, data evaluations are carried out using familiar tools such as Microsoft Excel. Simple relationships and patterns can be identified and included in the decision-making process. This level of maturity is already sufficient to meet normative requirements, such as those set out in DIN EN ISO 9001. However, modern solutions and tools offer much more far-reaching possibilities for increasing the value contribution of quality management.
At the ‘defined’ maturity level, data can be collected in real time, integrated with each other and evaluated automatically. Data silos are eliminated, dependencies and correlations become transparent. It becomes possible to analyse why certain events occur in a targeted manner.
The ‘managed’ maturity level goes one step further and enables a view into the future through the use of AI-based solutions.
At the ‘optimised’ level of maturity, data is used for simulations and analyses of individual options for action. Information is used proactively to make strategic and forward-looking decisions.
Conclusion: data – the heart of an effective QM system
Data and quality management belong together. Companies that know how to use their data effectively in quality management can achieve added value that goes far beyond mere compliance with standards.
Not only are they able to continuously and objectively evaluate the quality of processes and products, but they can also optimise them with an eye to the future and respond proactively to market requirements.
Data is the key to developing a real competitive advantage from a standardised QM system. Used cleverly, it creates full transparency and control for sustainable success.
In short, data is the game changer in modern quality management.
You can find more exciting topics from the world of adesso in our previous blog posts.
Do you want to determine how data-driven your quality management already is and what potential still exists? An audit that focuses on the effective collection and use of data along your value chain is the perfect introduction to data-driven quality management. Feel free to contact us and start the journey to effective quality management with us!